Tungsten Carbide Hammer Blade With Single Hole
Surface Hardening
Tungsten carbide alloy is overlaid on the working edges of the hammer blade, with a layer thickness of 1 to 3 mm. According to the test results, the service life of stacked welded tungsten carbide alloy hammer blades is 7~8 times higher than that of 65Mn overall quenched hammer blades, but the manufacturing cost of the former is more than twice as high.
Machining Accuracy
The hammer is a high-speed running part, and its manufacturing accuracy has a great influence on the balance of the pulverizer rotor. It is generally required that the mass difference between any two groups of hammers on the rotor should not exceed 5g. Therefore, the accuracy of the hammer must be strictly controlled during the processing process, especially for surfacing tungsten carbide hammers, the quality of the surfacing process must be strictly guaranteed. Hammer blades should be installed in sets, and random exchange between sets is not allowed.
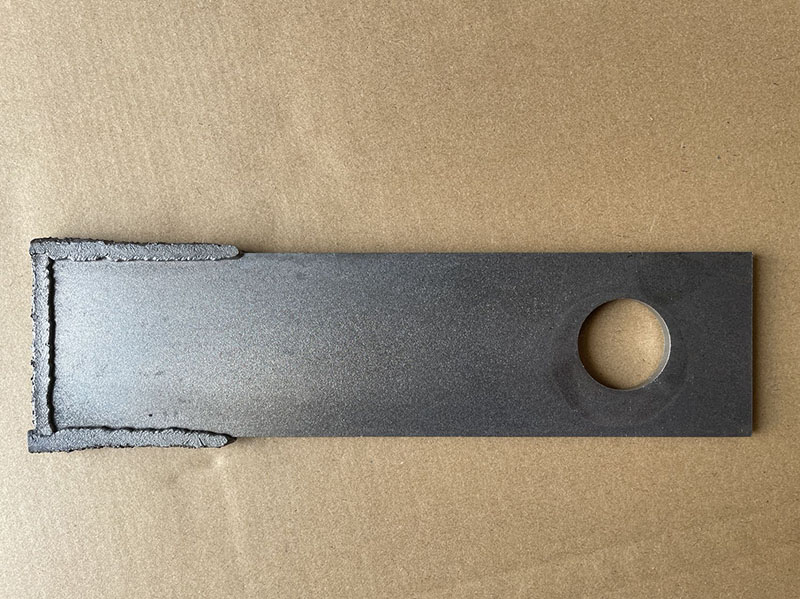
Quantity and Arrangement
The number and arrangement of hammer blades on the rotor of the hammer mill affect the balance of the rotor, the distribution of materials in the crushing chamber, the uniformity of hammer wear, and the efficiency of the crusher.
The number of hammer blades is measured by the number of hammer blades per unit of rotor width (hammer density), the density is too large for the rotor to start the torque, the material is struck more times, and the kWh output is reduced; the density is too small for the crusher output will be affected.
The arrangement of the hammer blades refers to the relative position relationship between groups of hammer blades on the rotor and between the same group of hammer blades. The arrangement of the hammer blades is best to achieve the following requirements: when the rotor rotates, the trajectory of each hammer blade does not repeat; the material does not shift to one side in the crushing chamber under the hammer blades (except for special requirements); the rotor is balanced in terms of force and does not vibrate at high speed.
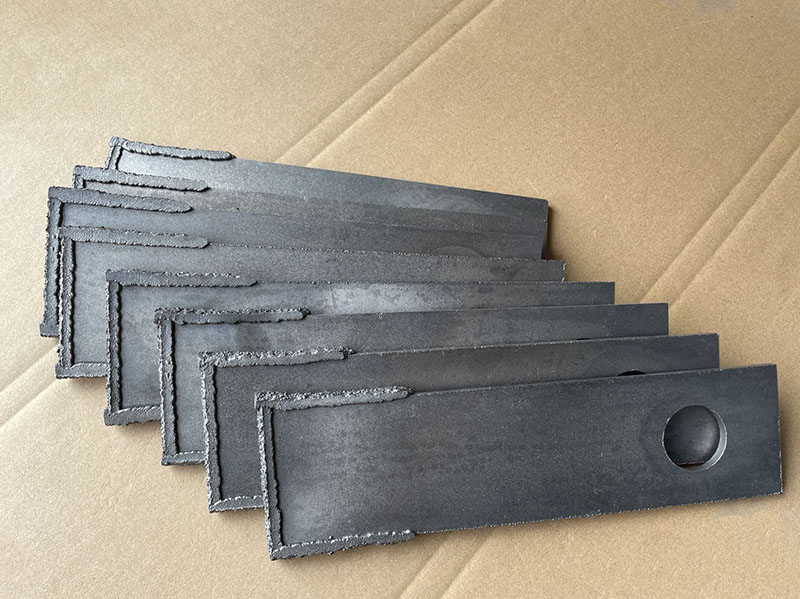
Working Principle
A group of hammer blades rotates through power conduction, and after reaching a certain speed, the material fed into the machine will be crushed (big broken small), and under the action of the fan, the crushed material will be discharged from the machine through the holes of the screen.
Product Replacement
The hammer blade is a working part of the crusher that directly strikes the material, and is therefore the fastest wearing and most frequently replaced wearing part. When the four working angles of the hammer blades are worn out, they should be replaced in time.
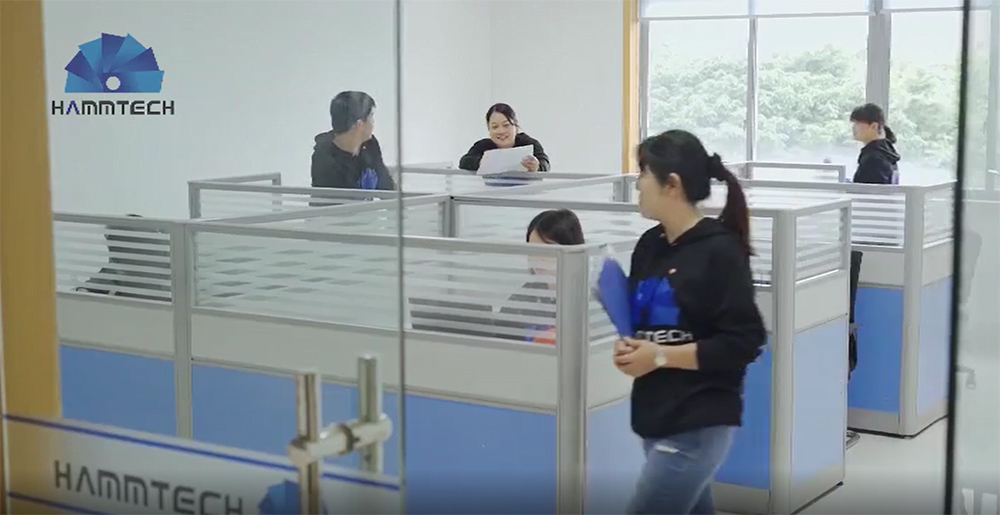
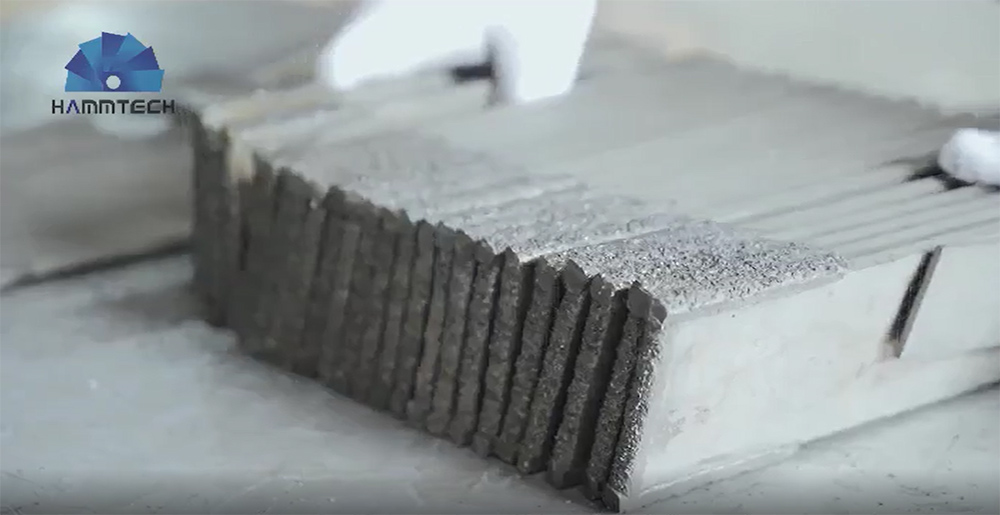

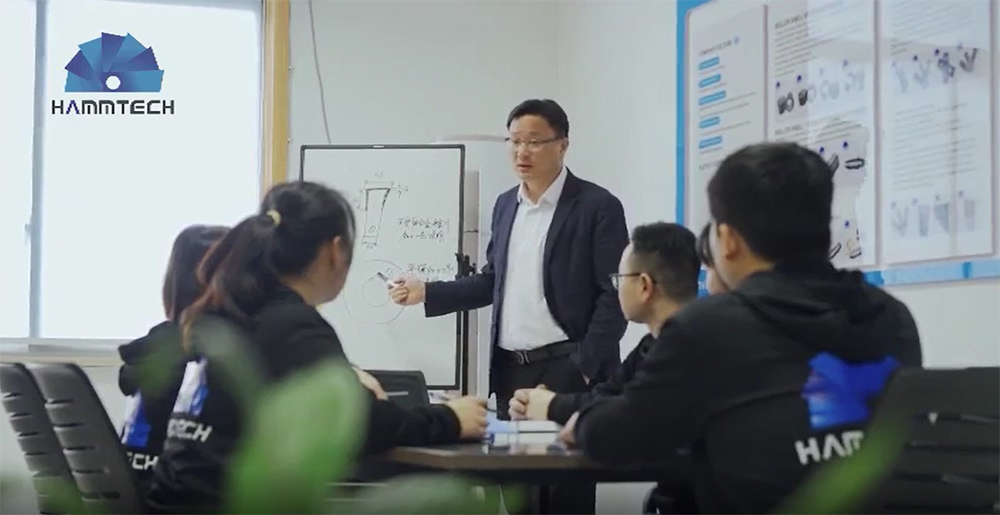
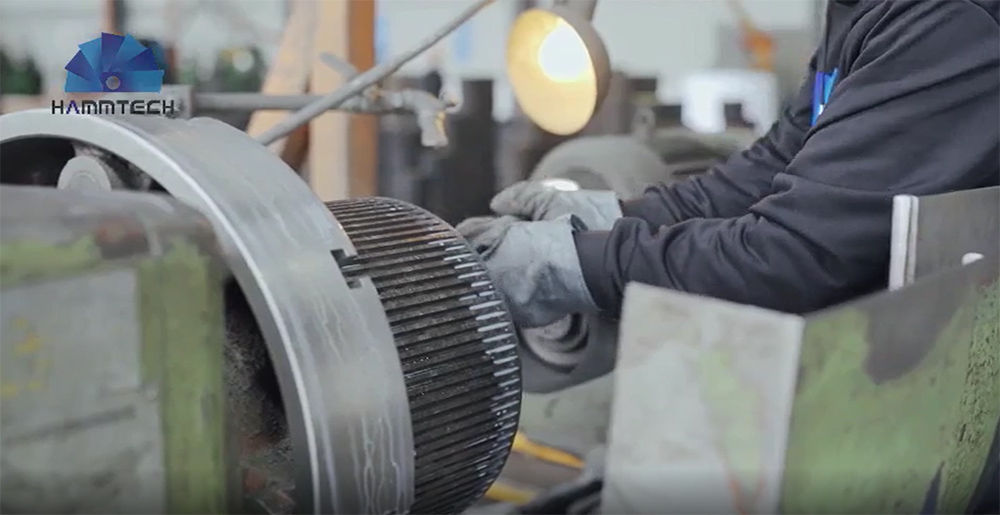
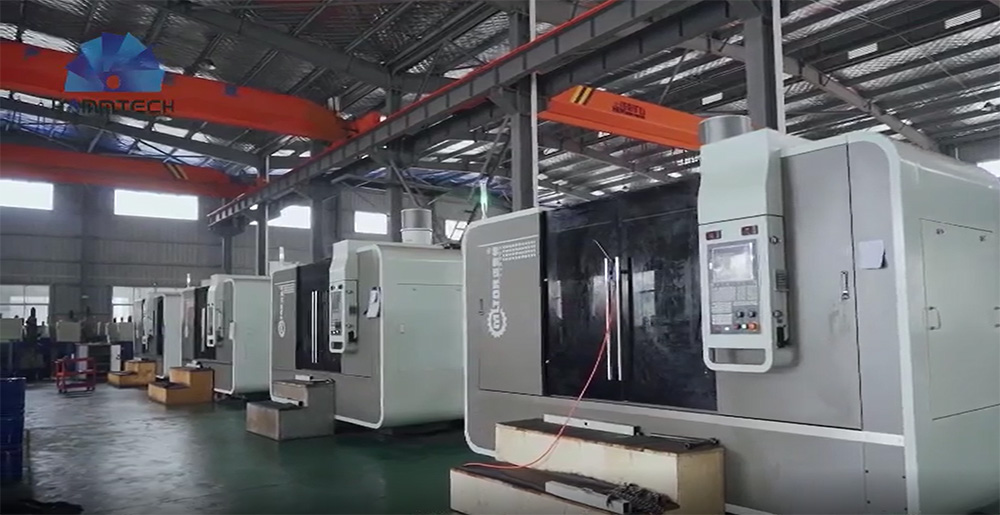