Abstract: In recent years, with the increasing emphasis on agriculture in China, the breeding industry and feed processing machinery industry have also experienced rapid development. This not only involves large-scale breeding farms, but also a large number of specialized farmers. Although China's basic research on feed processing machinery is close to the level of developed countries abroad, the relatively backward industrialization level seriously affects the sustained and healthy development of China's feed processing machinery industry. Therefore, this article deeply analyzes the safety hazards of feed processing machinery and proposes targeted preventive measures to further promote the continuous development of the feed processing machinery industry.
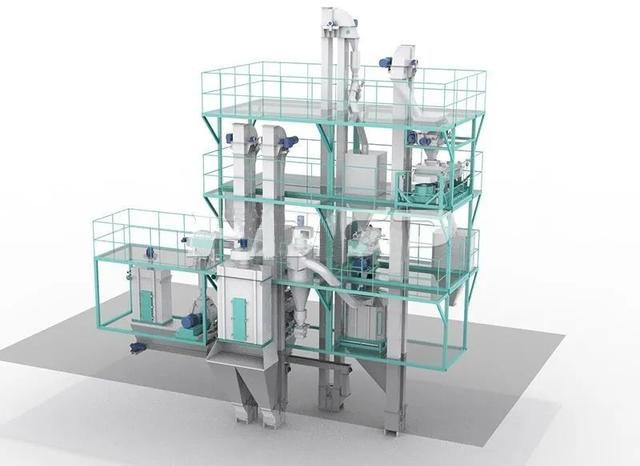
Analysis of the Future Supply and Demand Trends of Feed Processing Machinery
In recent years, China's aquaculture industry has been continuously developing, which has driven the continuous development of the feed processing industry. In addition, there are increasing requirements for feed processing machinery. This not only requires feed machinery to better meet production demands, but also puts forward relatively high requirements for mechanical equipment reliability and energy efficiency. At present, feed processing machinery enterprises in China are gradually moving towards large-scale and group oriented development, most of which utilize the business philosophy of integrating electromechanical, process, and civil engineering. This not only has the level of undertaking turnkey projects, but also brings a one-stop service. These have greatly driven the improvement of China's technological level and output. At the same time, we also need to fully recognize that there are still many problems with feed processing machinery and equipment in China. Although some machinery and equipment may have reached the international advanced development level, these enterprises are still relatively few for the entire industry. In the long run, these factors directly affect the sustainable and healthy development of feed processing enterprises.
Analysis of safety hazards in feed processing machinery and equipment
2.1 Lack of safety cover for flywheel
At present, the flywheel lacks a safety cover. Although most equipment is equipped with a safety cover, there are still many safety hazards in handling local details. During the work process, if accidents are not handled carefully or in urgent situations, it can cause the staff's clothing to enter the high-speed rotating belt. In addition, it can also cause the obligation to fall into the belt to be thrown to the on-site staff along with the running belt, resulting in certain injuries
2.2 Unscientific length of the feeding port bearing plate
Due to the unscientific length of the loading plate at the feeding port, metal objects, especially iron impurities such as gaskets, screws, and iron blocks, are stored in the raw materials obtained through automatic feeding mechanical transmission. Feed quickly enters the crusher, which then breaks the hammer and screen pieces. In severe cases, it will directly puncture the machine body, posing a serious threat to the life safety of resonance personnel.
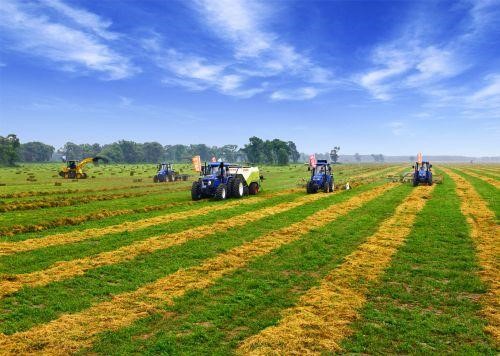
2.3 Lack of dust cover at the small material inlet
The small feeding port is filled with milling particle raw materials, such as vitamin additives, mineral additives, and so on. These raw materials are prone to dust before being mixed into the mixer, which can be absorbed by people. If people inhale these substances for a long time, they will experience nausea, dizziness, and chest tightness, which can seriously affect human health. In addition, when dust enters the motor and other equipment, it is easy to damage the components of the motor and other equipment. When some combustible dust accumulates at a certain concentration, it is easy to cause dust explosions and bring significant harm.
2.4 Mechanical vibration and blockage
We use a crusher as a case study to analyze mechanical vibration and blockage. Firstly, the crusher and motor are directly connected. When various factors cause electrons to be present in the rotor during assembly, as well as when the rotor of the crusher is not concentric, vibration problems may occur during the operation of the feed crusher. Secondly, when the crusher runs for a long time, there will be significant wear between the bearings and the shaft, resulting in the two support seats of the supporting shaft not being at the same center. During the work process, vibration will occur. Thirdly, the hammer blade may break or hard debris may occur in the crushing chamber. These will cause the rotor of the crusher to rotate unevenly,. This in turn causes mechanical vibration. Fourthly, the anchor bolts of the crusher are loose or the foundation is not firm. When adjusting and repairing, it is necessary to tighten the anchor bolts evenly. Shock-absorbing devices can be installed between the foundation and the crusher to reduce vibration effects. Fifthly, there are three factors that can cause blockages in the crusher: firstly, there is a relatively high moisture content in the raw materials. Secondly, the sieve is damaged and the hammer blades are cracked. Thirdly, the operation and use are unreasonable. When the crusher encounters blockage issues, it not only affects productivity, such as severe blockage, but also causes overload and even burns out the motor, requiring immediate shutdown.
2.5 Burns caused by high temperature factors
Because the process requirements of the puffing equipment need to be in high temperature and high humidity environments, it needs to be connected to high-temperature steam pipelines. Due to the chaotic layout of pipeline design and on-site installation, steam and high-temperature water pipelines are often exposed, causing personnel to suffer from burns and other problems. In addition, extrusion and tempering equipment have relatively high internal temperatures, as well as high temperatures on the surface and discharge doors, which can easily lead to high-temperature burns and other situations.
3 Safety protection measures for feed processing machinery
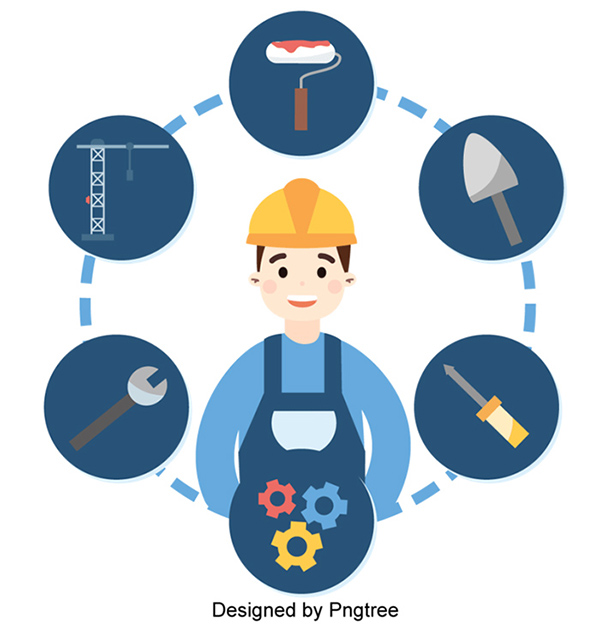
3.1 Optimization of Purchasing Processing Machinery
Firstly, the crusher. At present, crushers are a commonly used type of feed processing machinery equipment. The main types of mechanical equipment in our country are roller crusher and hammer crusher. Crush the raw materials into particles of different sizes according to different feeding requirements. Secondly, the mixer. There are two main types of conventional feed mixers, namely horizontal and vertical. The advantage of a vertical mixer is that the mixing is uniform and there is relatively little power consumption. Its shortcomings include a relatively long mixing time, low production efficiency, and insufficient discharge and loading. The advantages of a horizontal mixer are high efficiency, rapid discharge, and loading. Its drawback is that it consumes a considerable amount of power and occupies a large area, resulting in a high price. Thirdly, there are two main types of elevators, namely spiral elevators and bucket elevators. Usually, spiral elevators are used. Fourthly, the puffing machine. It is a processing equipment that integrates cutting, cooling, mixing, and forming processes, mainly including wet puffing machines and dry puffing machines.
3.2 Pay special attention to the installation process
Normally, the installation sequence of the feed processing unit is to first install the crusher, and then install the electric motor and transmission belt. The mixer needs to be installed next to the crusher, so that the discharge port of the crusher is connected to the inlet port of the mixer. Connect the elevator to the inlet of the crusher. During the processing, the main raw materials are poured into the pit, and the elevator lifts the raw materials into the crusher for crushing. Then, they enter the mixing bin of the mixer. Other raw materials can be directly poured into the mixing bin through the feeding port.
3.3 Effective Control of Common Problems
Firstly, in case of abnormal mechanical vibration, the left and right positions of the motor or the addition of pads can be adjusted, thereby adjusting the concentricity of the two rotors. Place a thin copper sheet on the bottom surface of the supporting shaft seat, and add adjustable wedges at the bottom of the bearing seat to ensure concentricity of the bearing seat. When replacing the hammer blade, the difference in quality should not exceed 20 grams, in order to ensure static balance and prevent vibration of the unit. When maintaining and adjusting the equipment, it is necessary to tighten the anchor bolts evenly. Shock-absorbing devices can be installed between the foundation and the crusher to reduce vibration. Secondly, when blockage occurs, it is necessary to first clear the discharge port, replace the mismatched conveying equipment, and then adjust the feeding amount reasonably to ensure the normal operation of the equipment. Check if the moisture content of the raw materials is too high. The material moisture content of the crusher needs to be lower than 14%. If materials with high moisture content cannot enter the crusher.
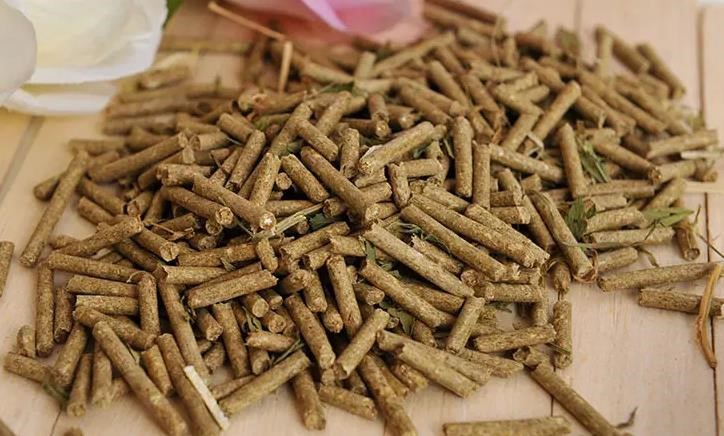
Conclusion
In recent years, with the continuous development of the breeding industry, the feed processing industry has experienced rapid growth, which has further promoted the continuous progress of the thinking machinery industry. At present, although the feed machinery industry in China has made continuous progress through the use of modern technology, there are still many problems in the application process of products, and many equipment even contain serious safety hazards. On this basis, we need to pay extra attention to these issues and fully prevent safety hazards.
Post time: Jan-11-2024