Poor water resistance, uneven surface, high powder content, and uneven length? Common problems and improvement measures in aquatic feed production
In our daily production of aquatic feed, we have encountered some problems from various aspects. Here are some examples to discuss with everyone, as follows:
1、 Formula
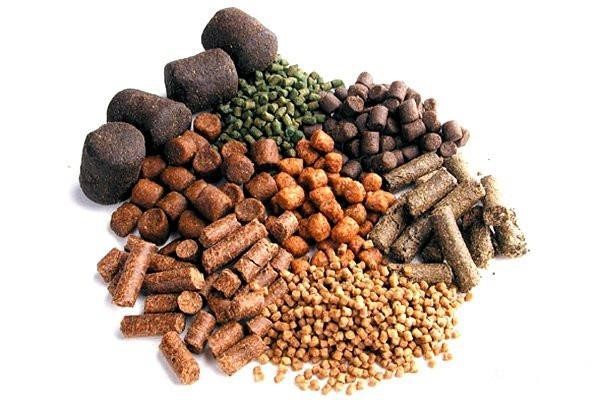
1. In the formula structure of fish feed, there are more types of meal raw materials, such as rapeseed meal, cotton meal, etc., which belong to crude fiber. Some oil factories have advanced technology, and the oil is basically fried dry with very little content. Moreover, these types of raw materials are not easily absorbent in production, which has a lot of impact on granulation. In addition, cotton meal is difficult to crush, which affects efficiency.
2. Solution: The use of rapeseed cake has been increased, and high-quality local ingredients such as rice bran have been added to the formula. Additionally, wheat, which accounts for approximately 5-8% of the formula, has been added. Through adjustment, the granulation effect in 2009 is relatively ideal, and the yield per ton has also increased. The 2.5mm particles are between 8-9 tons, an increase of nearly 2 tons compared to the past. The appearance of the particles has also significantly improved.
In addition, to improve the efficiency of crushing cottonseed meal, we mixed cottonseed meal and rapeseed meal in a 2:1 ratio before crushing. After improvement, the crushing speed was basically on par with the crushing speed of rapeseed meal.
2、 Uneven surface of particles
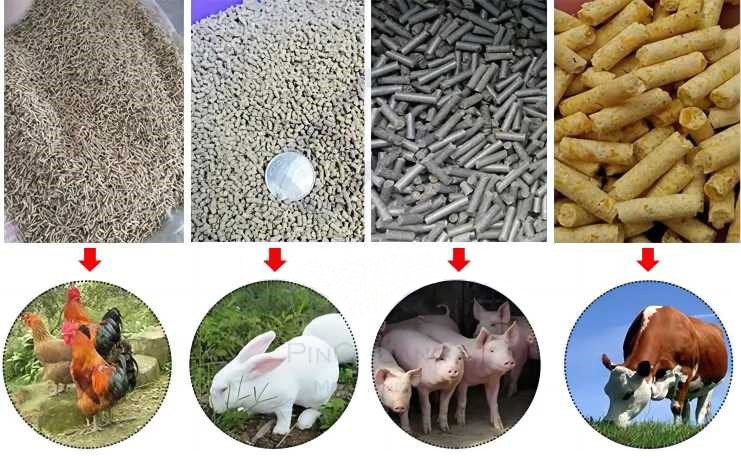
1. It has a great impact on the appearance of the finished product, and when added to water, it is prone to collapse and has a low utilization rate. The main reason is:
(1) The raw materials are crushed too coarse, and during the tempering process, they are not fully matured and softened, and cannot be well combined with other raw materials when passing through the mold holes.
(2) In the fish feed formula with a high content of crude fiber, due to the presence of steam bubbles in the raw material during the tempering process, these bubbles rupture due to the pressure difference between inside and outside the mold during particle compression, resulting in uneven surface of the particles.
2. Handling measures:
(1) Control the crushing process properly
At present, when producing fish feed, our company uses 1.2mm sieve micro powder as the bulk raw material. We control the frequency of use of the sieve and the degree of wear of the hammer to ensure the fineness of crushing.
(2) Control steam pressure
According to the formula, adjust the steam pressure reasonably during production, generally controlling around 0.2. Due to the large amount of coarse fiber raw materials in the fish feed formula, high-quality steam and reasonable tempering time are required.
3、 Poor water resistance of particles
1. This type of problem is the most common one in our daily production, generally related to the following factors:
(1) Short tempering time and low tempering temperature result in uneven or insufficient tempering, low ripening degree, and insufficient moisture.
(2) Insufficient adhesive materials such as starch.
(3) The compression ratio of the ring mold is too low.
(4) The oil content and the proportion of crude fiber raw materials in the formula are too high.
(5) Crushing particle size factor.
2. Handling measures:
(1) Improve steam quality, adjust the blade angle of the regulator, extend the tempering time, and appropriately increase the moisture content of the raw materials.
(2) Adjust the formula, appropriately increase starch raw materials, and reduce the proportion of fat and crude fiber raw materials.
(3) Add adhesive if necessary. (Sodium based bentonite slurry)
(4) Improve the compression ratio of the ring die
(5) Control the fineness of crushing well
4、 Excessive powder content in particles
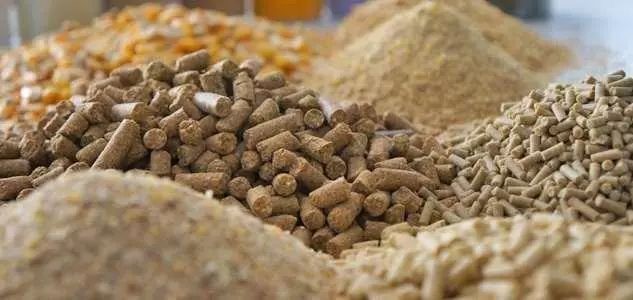
1. It is difficult to ensure the appearance of general pellet feed after cooling and before screening. Customers have reported that there are more fine ash and powder in the pellets. Based on the above analysis, I think there are several reasons for this:
A. The particle surface is not smooth, the incision is not neat, and the particles are loose and prone to powder production;
B. Incomplete screening by grading screen, clogged screen mesh, severe wear of rubber balls, mismatched screen mesh aperture, etc;
C. There is a lot of fine ash residue in the finished product warehouse, and the clearance is not thorough;
D. There are hidden dangers in dust removal during packaging and weighing;
Handling measures:
A. Optimize the formula structure, select the ring die reasonably, and control the compression ratio well.
B. During the granulation process, control the tempering time, feeding amount, and granulation temperature to fully ripen and soften the raw materials.
C. Ensure that the particle cross-section is neat and use a soft cutting knife made of steel strip.
D. Adjust and maintain the grading screen, and use a reasonable screen configuration.
E. The use of secondary screening technology under the finished product warehouse can greatly reduce the powder content ratio.
F. It is necessary to clean the finished product warehouse and circuit in a timely manner. In addition, it is necessary to improve the packaging and dust removal device. It is best to use negative pressure for dust removal, which is more ideal. Especially during the packaging process, the packaging worker should regularly knock and clean the dust from the buffer hopper of the packaging scale.
5、 Particle length varies
1. In daily production, we often encounter difficulties in control, especially for models above 420. The reasons for this are roughly summarized as follows:
(1) The feeding amount for granulation is uneven, and the tempering effect fluctuates greatly.
(2) Inconsistent gap between the mold rollers or severe wear of the ring mold and pressure rollers.
(3) Along the axial direction of the ring mold, the discharge speed at both ends is lower than that in the middle.
(4) The pressure reducing hole of the ring mold is too large, and the opening rate is too high.
(5) The position and angle of the cutting blade are unreasonable.
(6) Granulation temperature.
(7) The type and effective height (blade width, width) of the ring die cutting blade have an impact.
(8) At the same time, the distribution of raw materials inside the compression chamber is uneven.
2. The quality of feed and pellets is generally analyzed based on their internal and external qualities. As a production system, we are more exposed to things related to the external quality of feed pellets. From a production perspective, the factors that affect the quality of aquatic feed pellets can be roughly summarized as follows:
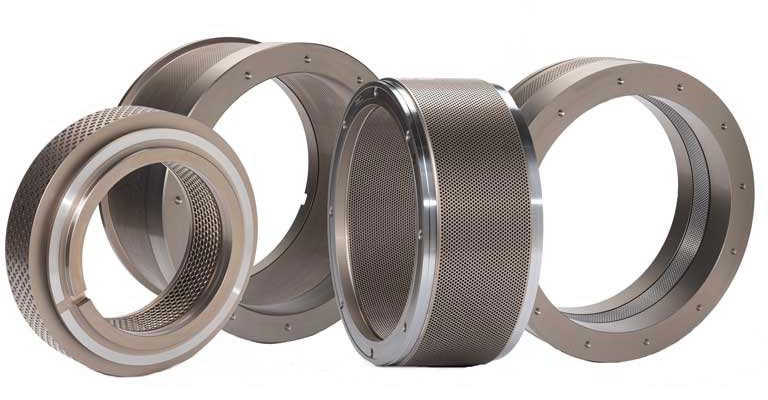
(1) The design and organization of formulas have a direct impact on the quality of aquatic feed pellets, accounting for approximately 40% of the total;
(2) The intensity of crushing and the uniformity of particle size;
(3) The diameter, compression ratio, and linear velocity of the ring mold have an impact on the length and diameter of particles;
(4) The compression ratio, linear velocity, quenching and tempering effect of the ring mold, and the influence of the cutting blade on the length of the particles;
(5) The moisture content of raw materials, tempering effect, cooling and drying have an impact on the moisture content and appearance of finished products;
(6) The equipment itself, process factors, and quenching and tempering effects have an impact on the particle powder content;
3. Handling measures:
(1) Adjust the length, width, and angle of the fabric scraper, and replace the worn scraper.
(2) Pay attention to adjusting the position of the cutting blade in a timely manner at the beginning and near the end of production due to the small feeding amount.
(3) During the production process, ensure stable feeding rate and steam supply. If the steam pressure is low and the temperature cannot rise, it should be adjusted or stopped in a timely manner.
(4) Reasonably adjust the gap between the roller shell. Follow the new mold with new rollers, and promptly repair the uneven surface of the pressure roller and ring mold due to wear.
(5) Repair the guide hole of the ring mold and promptly clean the blocked mold hole.
(6) When ordering the ring mold, the compression ratio of the three rows of holes at both ends of the axial direction of the original ring mold can be 1-2mm smaller than that in the middle.
(7) Use a soft cutting knife, with a thickness controlled between 0.5-1mm, to ensure a sharp edge as much as possible, so that it is on the meshing line between the ring mold and the pressure roller.
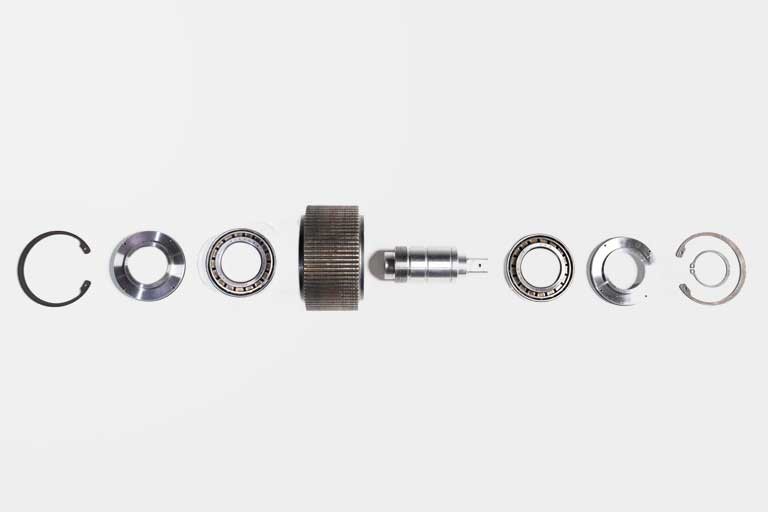
(8) Ensure the concentricity of the ring mold, regularly check the spindle clearance of the granulator, and adjust it if necessary.
6、 Summary Control points:
1. Grinding: The fineness of grinding must be controlled according to the specification requirements
2. Mixing: The uniformity of raw material mixing must be controlled to ensure appropriate mixing amount, mixing time, moisture content, and temperature.
3. Maturation: The pressure, temperature, and moisture of the puffing machine must be controlled
The size and shape of the particle material: appropriate specifications of compression molds and cutting blades must be selected.
5. Water content of finished feed: It is necessary to ensure the drying and cooling time and temperature.
6. Oil spraying: It is necessary to control the precise amount of oil spraying, the number of nozzles, and the quality of the oil.
7. Screening: Select the size of the sieve according to the specifications of the material.
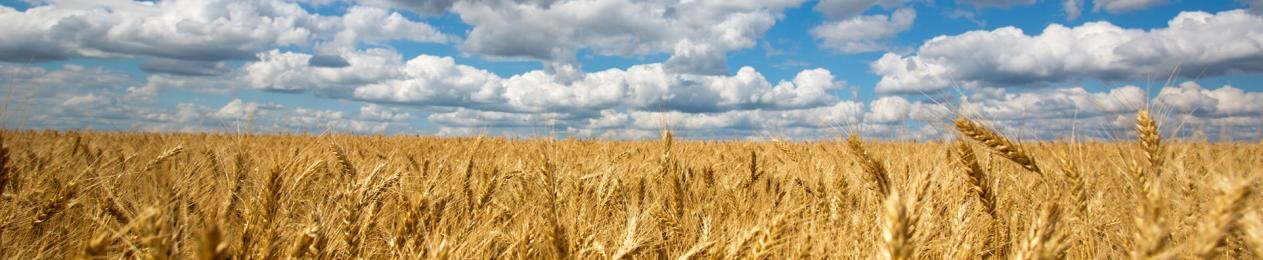
Post time: Nov-30-2023