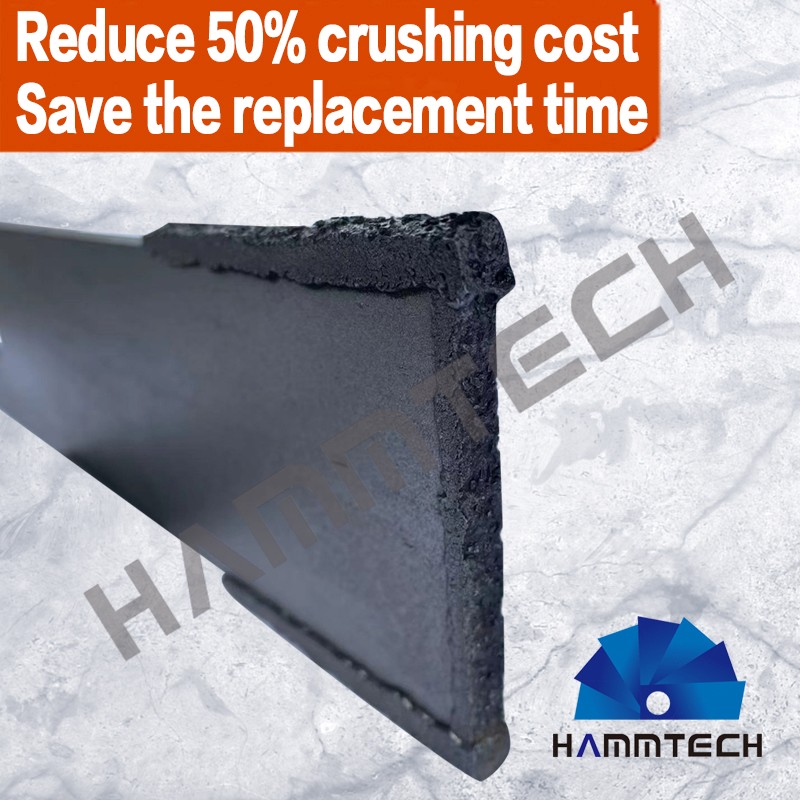
In many usage scenarios. There are not only requirements for the wear resistance of the hammer blade, but also very high requirements for the impact resistance of the hammer blade.
How to achieve both wear resistance and high impact resistance? HMT's tungsten carbide hammer blade perfectly solves this problem.
As is well known, tungsten carbide particles have high hardness. Achieve HRC72~75. Tungsten carbide hammer blades in the previous market. Adopting brazing or fiber welding techniques. Hammer blades are prone to detachment and cracking of hard alloys under high impact. There are many hammer pieces on the market. The problem is not that the wear-resistant layer is not wear-resistant, but that the wear-resistant layer falls off under high impact crushing.
HMT's fusion welding technology hammer integrates tungsten carbide particles with the hammer body, tightly bonding them together. tungsten carbide particles themselves have high wear resistance and hardness. It is equivalent to putting the highest quality armor on the hammer body, which is connected to the bloodline and will never cause the wear-resistant layer to fall off.
HMT’s tungsten carbide hammer blades are armor warriors with high impact resistance, wear resistance, and hardness.
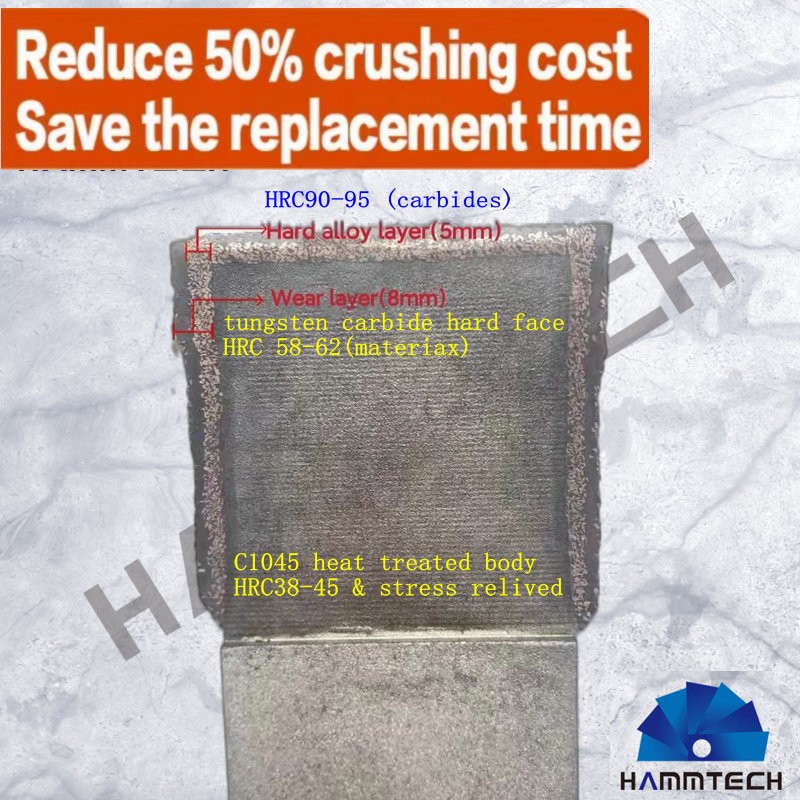
Post time: Mar-12-2025