Flat Die for Pellet Machine
Pellet Mill Flat Dies are commonly used components in pellet mills to compress materials such as wood or biomass into pellets. The flat die is constructed as a disc with small holes drilled into it. As the pellet mill's rollers push materials through a die, they are shaped into pellets. They are widely used for the production of aquatic pellet feeds: floating feeds, sinking feeds, suspension feeds.
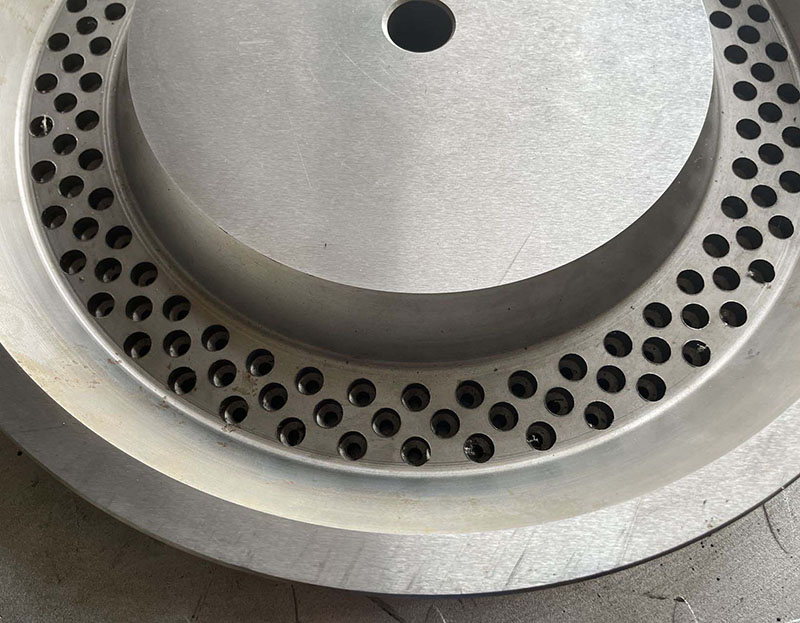
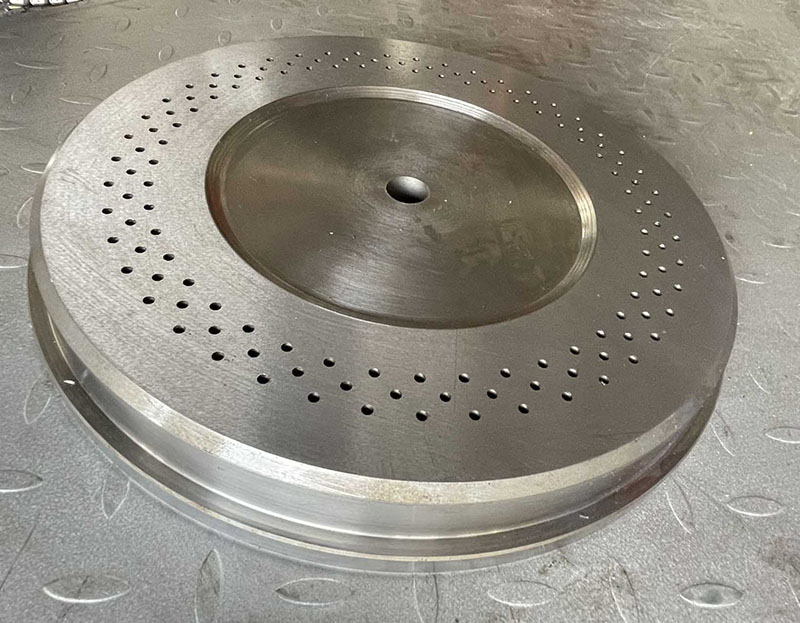
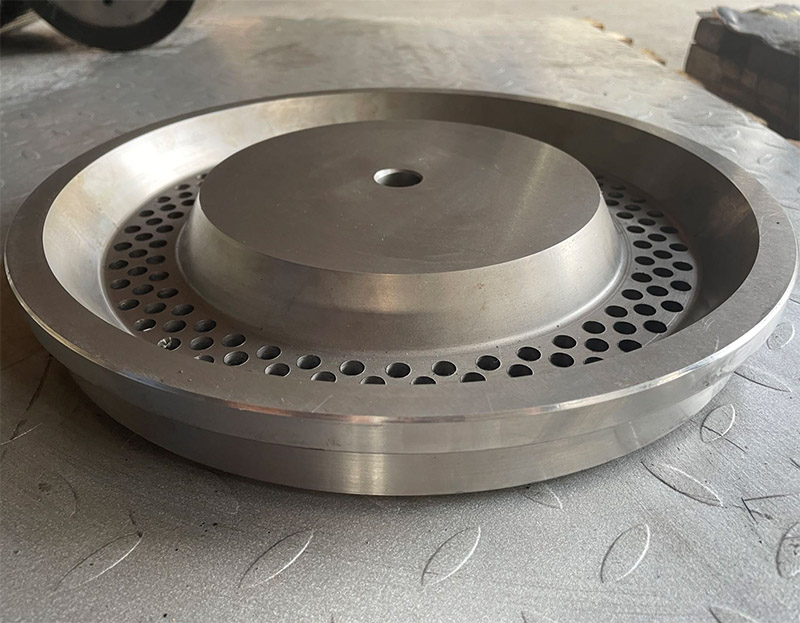
The first step in making a pellet mill flat die is choosing the steel plate you will be using. The plate must be made of high-quality hardened steel capable of withstanding the stresses created during the granulation process. Board thickness is also an important factor to consider. Thicker plates generally last longer, but require more power to run. Thinner plates, on the other hand, require less power but may wear out sooner.
Before you start drilling, you need to plan the design of the flat form. This will include determining the size and spacing of the holes required for the particles you wish to create. To draw the design on the steel plate, use a marker, ruler, and compass. You must be accurate when drawing your design, especially with regard to hole spacing. Once the design is drawn on the board, it's time to start drilling the holes. To do this, use a drill press with the appropriate drill bit. Depending on particle size and design, you may need to use a different size drill. Drill each hole slowly and carefully, making sure they are positioned correctly according to the design.
Once you've drilled all the holes in the steel plate, you'll want to make sure the mold is clean and free of any burrs that could damage the rollers. Clean the plate to remove any metal shavings and use a metal file to smooth any rough edges. Finally, give it a good polish to make sure it's smooth and free of blemishes.
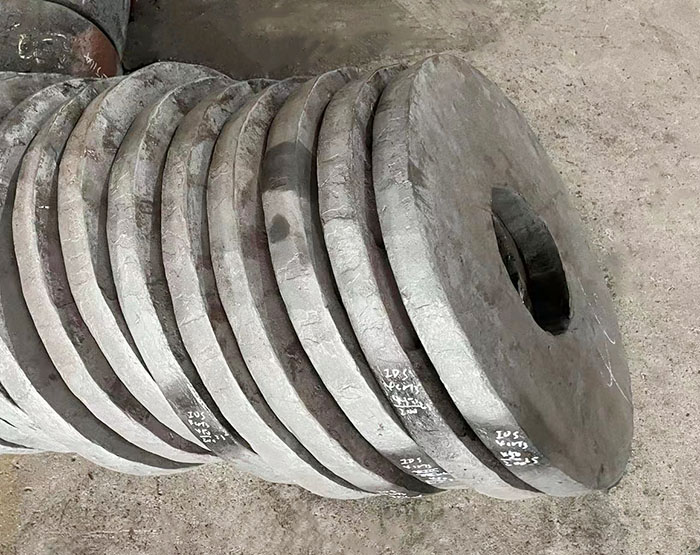
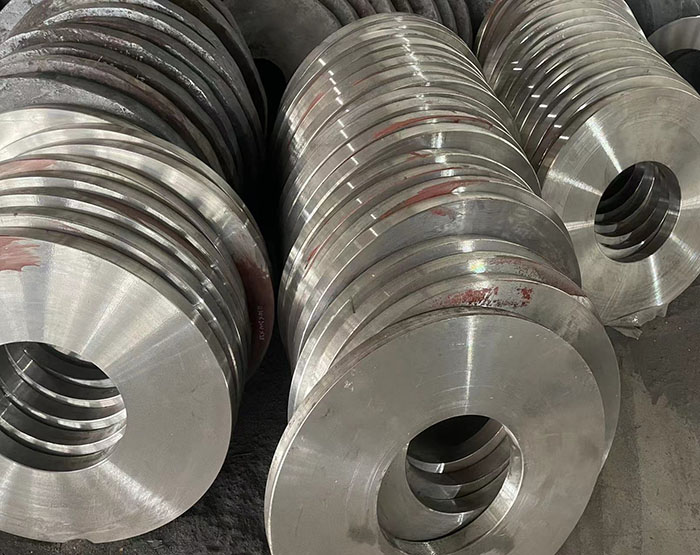
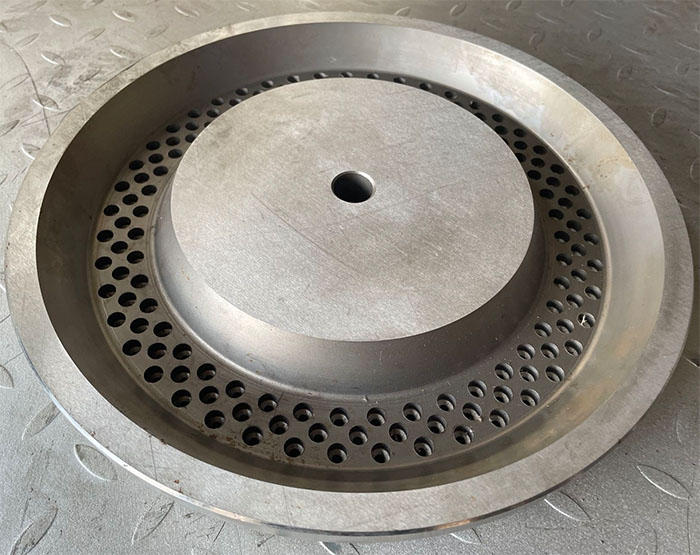
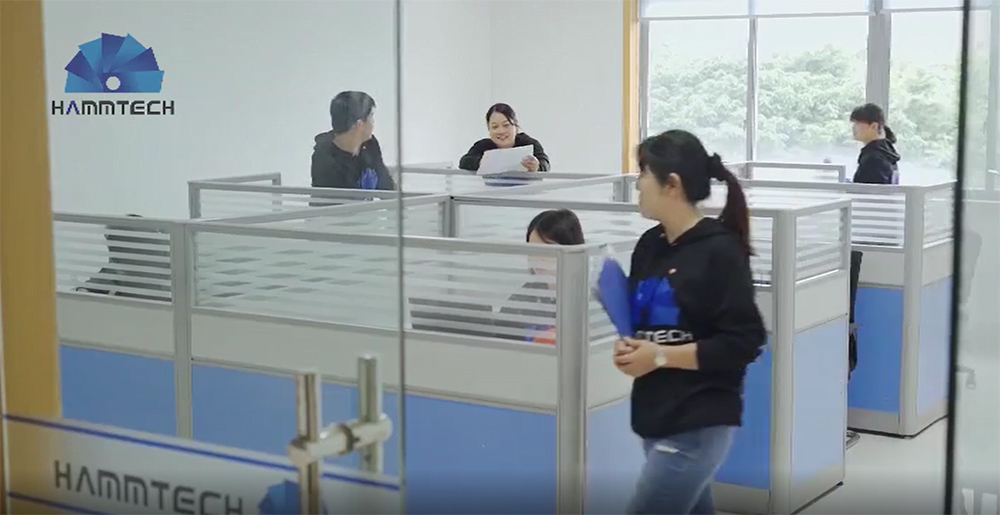
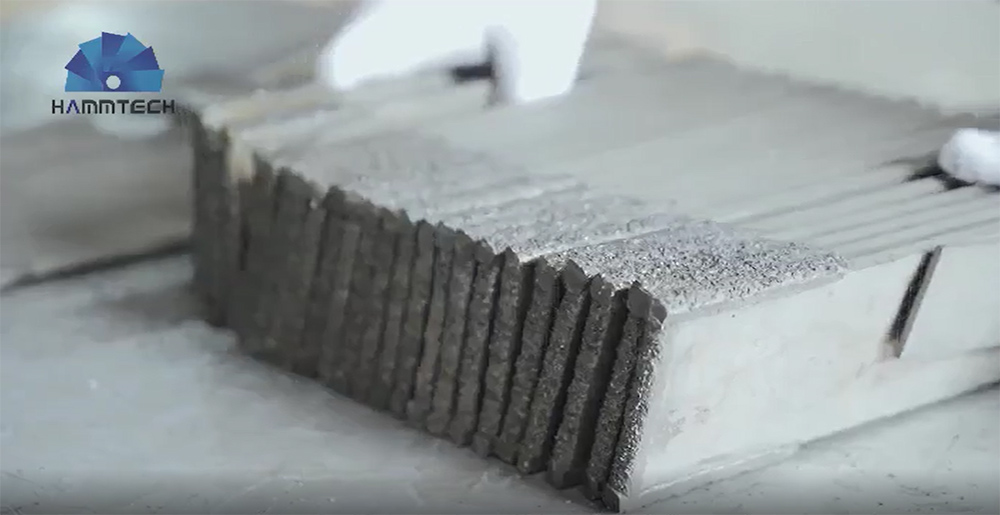

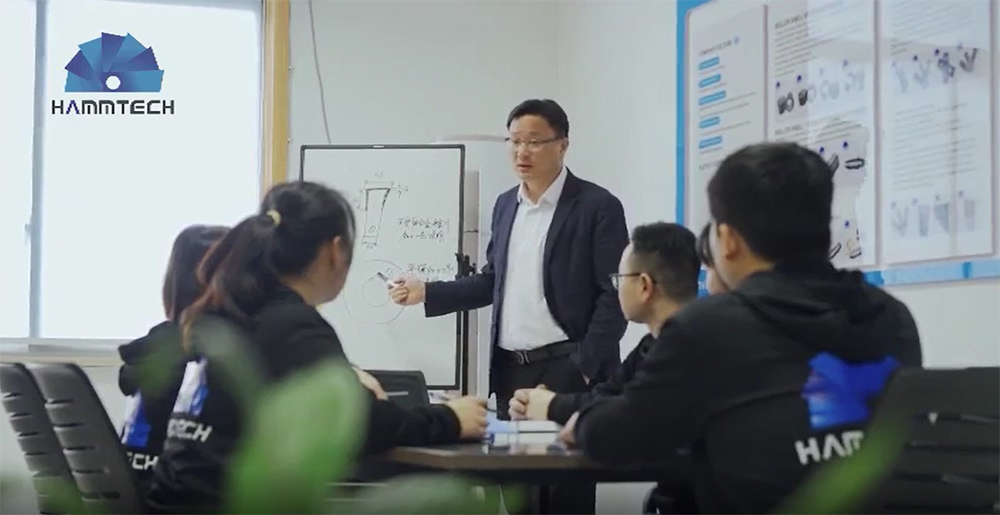
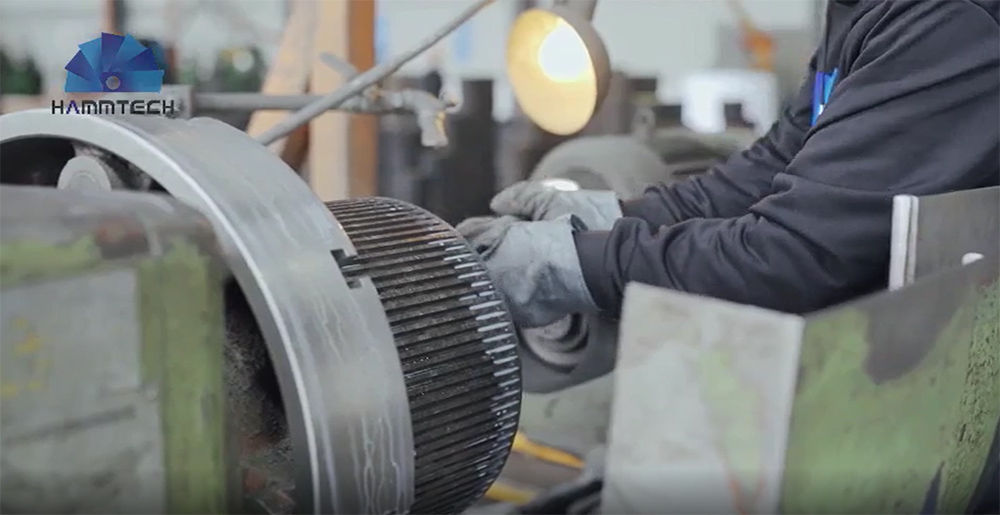
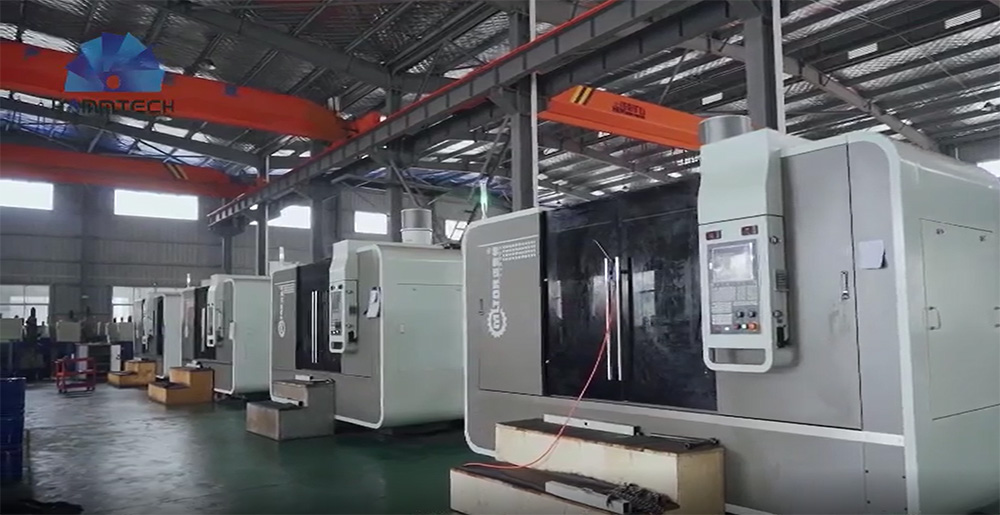