Double Teeth Roller Shell
The pellet mill roller shell is an important accessory of the pelletizer, which is also easy to wear as the ring die. It works mainly with the ring die and flat die to cut, knead, set, and squeeze the raw materials to achieve pelletizing. Roller shells are widely used for processing animal feed pellets, biomass fuel pellets, etc.
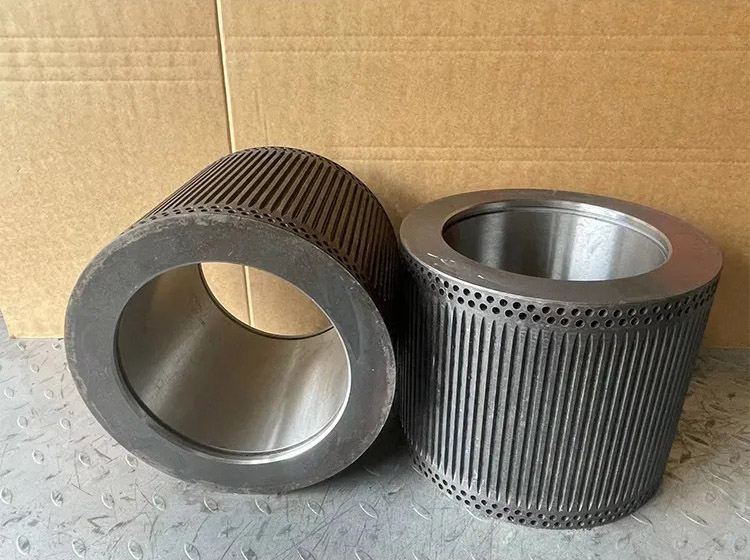
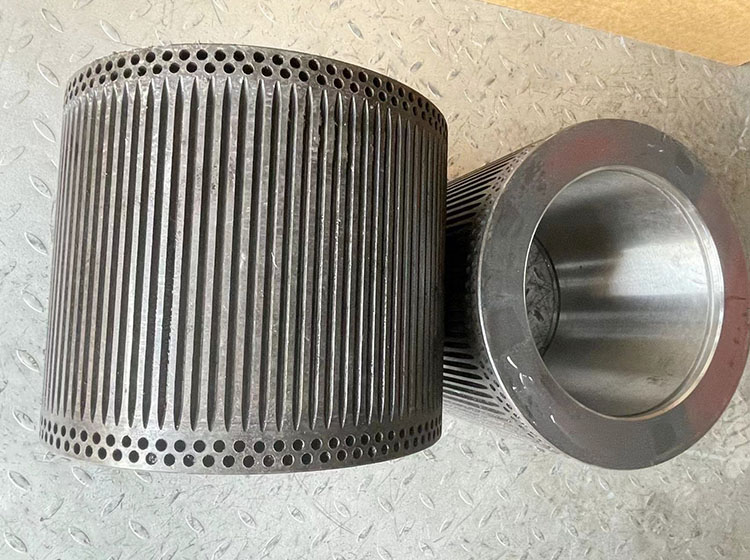
In the granulator process, in order to ensure that the raw material can be pressed into the die hole, there must be some friction between the roller shell and the material, so when making the roller shell, it will be designed with different forms of rough surfaces to prevent the roller from slipping. There are three kinds of surfaces that are most widely used: dimpled type, open-end type, and closed-end type.
Dimpled Roller Shell
The surface of a dimpled roller shell is like a honeycomb with cavities. In the process of use, the cavity is filled with material, forming a friction surface friction coefficient is small, the material is not easy to slide sideways, the wear of the ring die of the granulator is more uniform, and the length of the particles obtained is more consistent, but the roll material performance is slightly worse, there may be an impact on the yield of the granulator, in actual production is not as common as the open and closed-end types.
Open-end Roller Shell
It has a strong anti-slip ability and good roll material performance. However, in the production process, the material slides in the tooth groove, which may lead to the problem of material sliding towards one side, resulting in a certain difference in the wear of the roller shell and ring die. Generally, the wear is serious at the two ends of the roller shell and ring die, which will lead to the difficulty of discharging material at the two ends of the ring die for a long time, so the pellets made are shorter than the middle part of the ring die.
Closed-end Roller Shell
The two ends of this kind of roller shell are designed to be closed type(a toothed groove type with sealed edges). Due to the closed edges on both sides of the groove, the raw material is not easily sliding to both sides under extrusion, especially when used in the extrusion of aquatic materials which are more prone to sliding. This reduces this slippage and results in an even distribution of the material, more uniform wear of the roller shell and ring die, and thus a more uniform length of pellets.
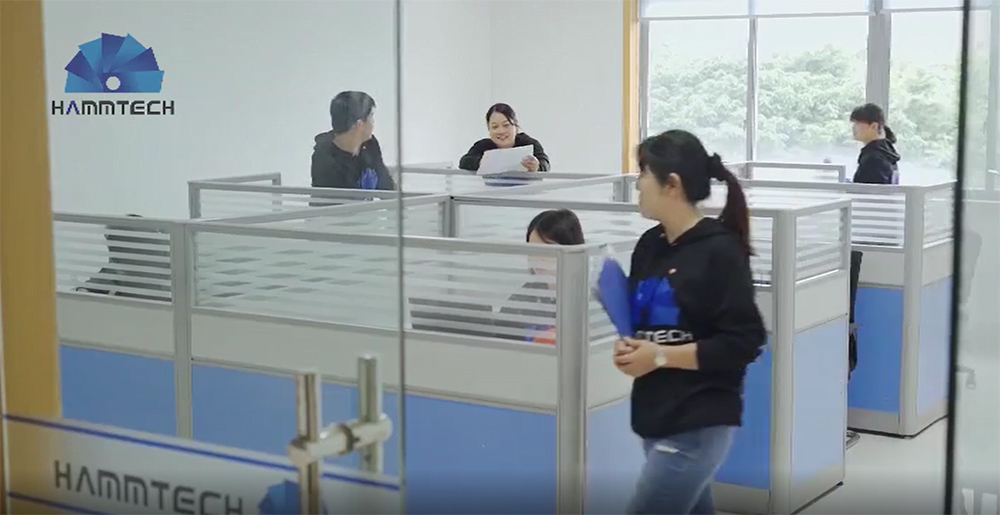
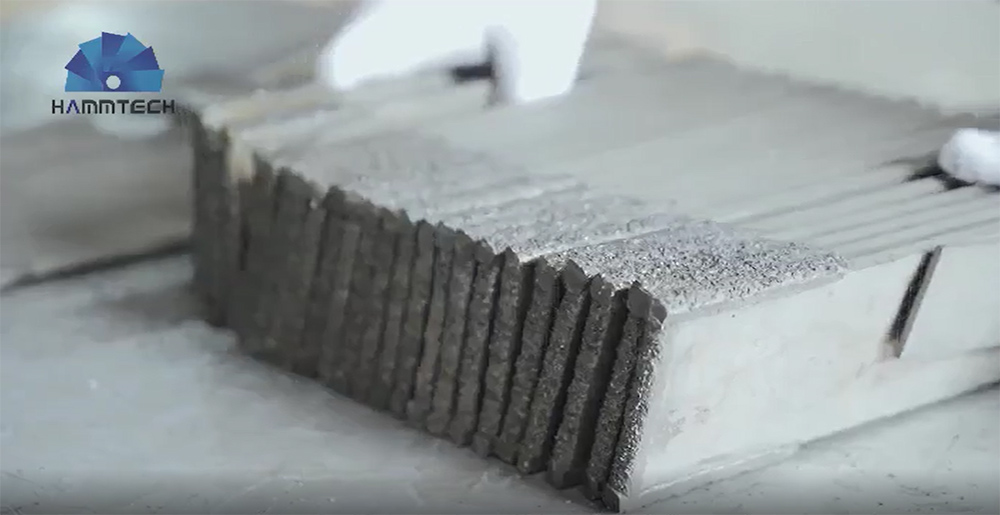

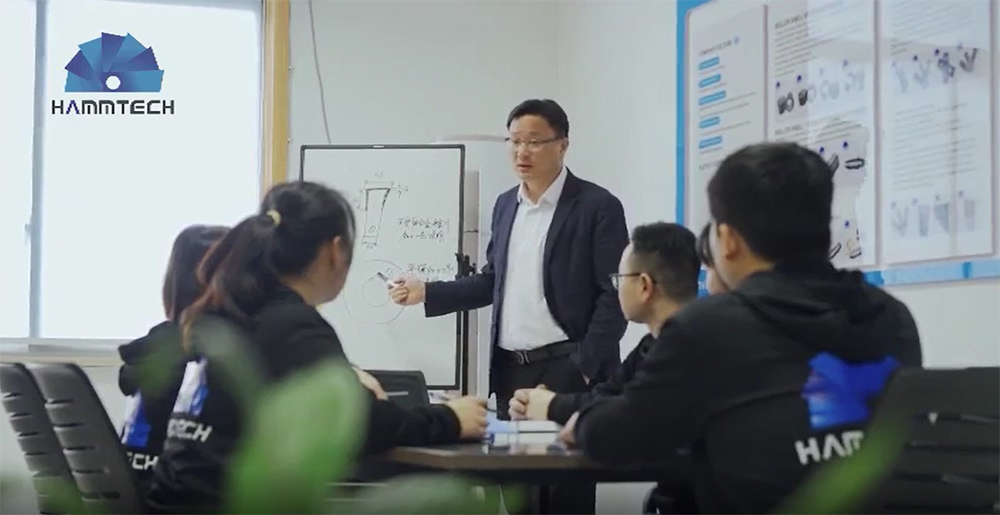
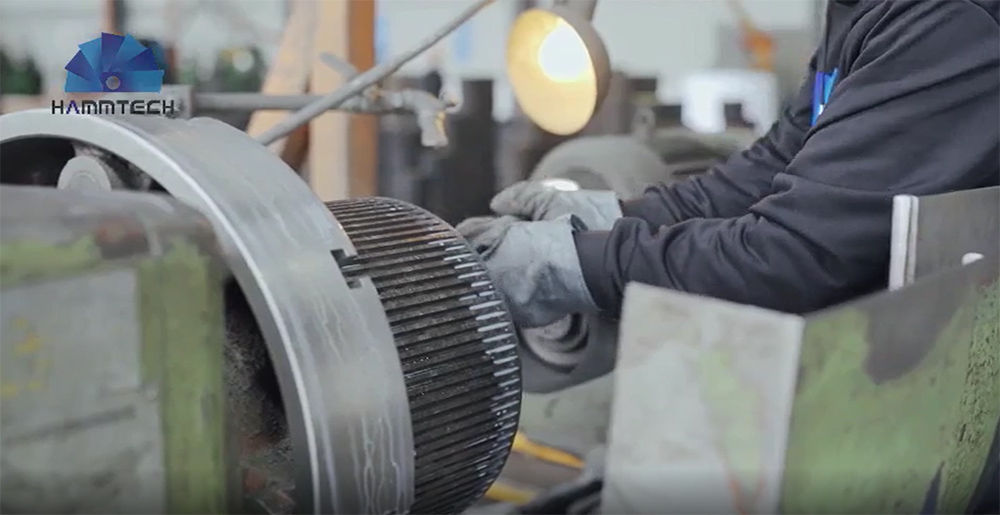
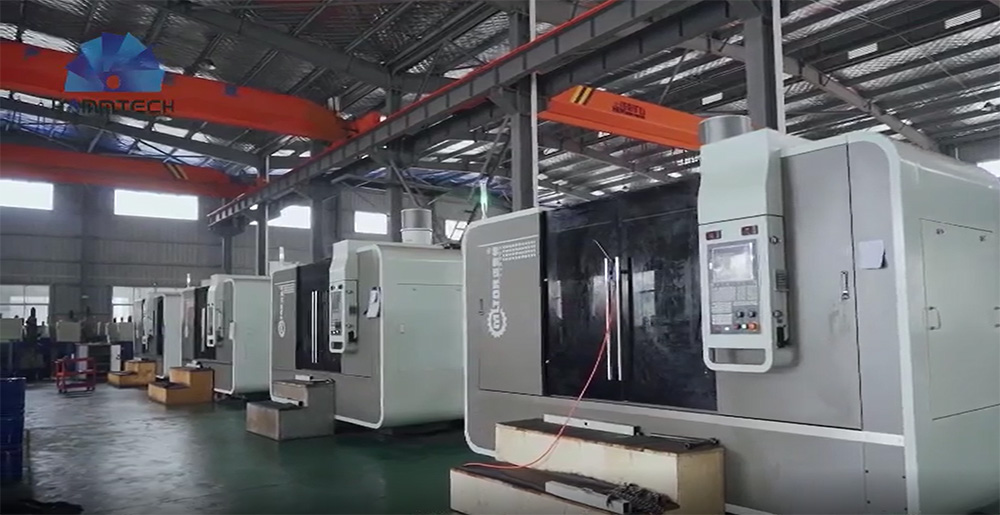