Circle Teeth Roller Shell
In the pellet production industry, ring die or flat die pelleting machines are commonly used to press powdered materials into pellet feed. Both flat and ring die rely on the relative movement of the pressure roller and the die to grab the material into an effective working position and squeeze it into shape. This pressure roller, commonly known as the pressure roller shell, is the key working part of the pellet mill, as with the ring die, and is also one of the wearing parts.
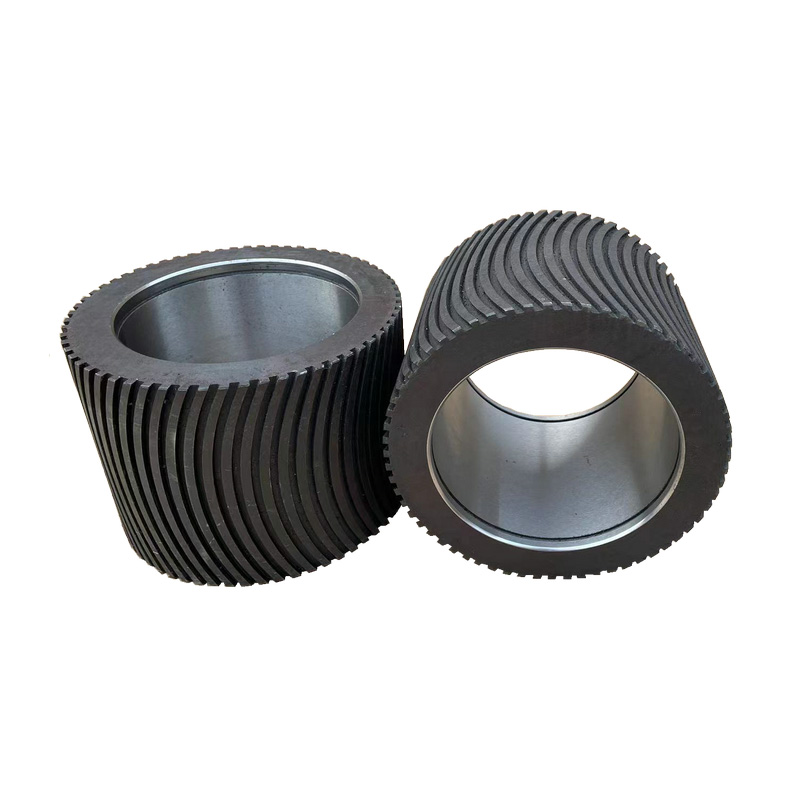
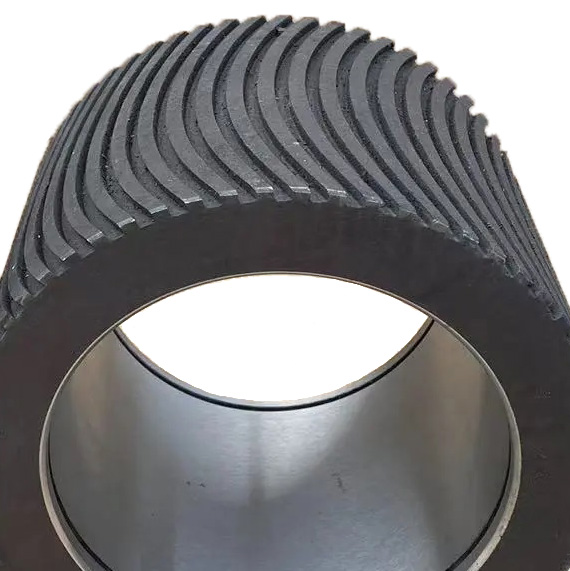
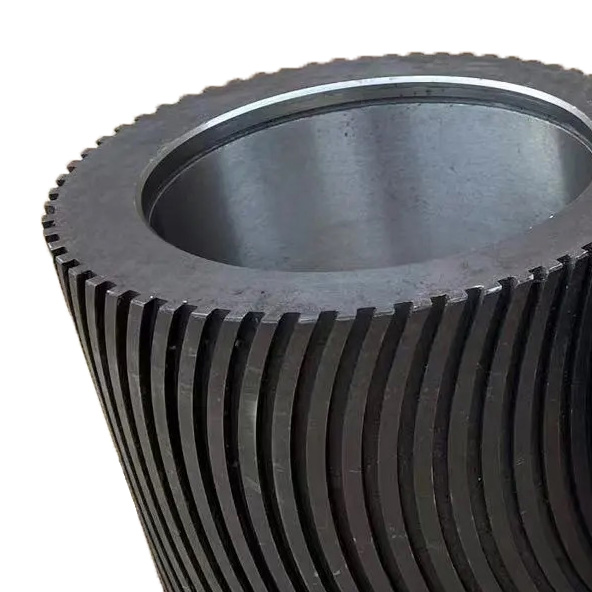
The pressure roller of the granulator is used to squeeze the material into the ring die. As the roller is subjected to friction and squeezing pressure for a long time, the outer circumference of the roller is machined into grooves, which enhances the resistance to wear and tear and makes it easy to grab the loose material.
The working conditions of the rollers are worse than those of the ring die. In addition to the normal wear of the raw material on the rollers, the silicate, SiO2 in the sand, iron filings, and other hard particles in the raw material intensify the wear on the rollers. As the linear velocity of the pressure roller and the ring die are basically equal, the diameter of the pressure roller is only 0.4 times the inner diameter of the ring die, so the wear rate of the pressure roller is 2.5 times higher than that of the ring die. For example, the theoretical design life of a pressure roller is 800 hours, but the actual use time is not more than 600 hours. In some factories, due to improper use, the use time is less than 500 hours, and the failed rollers can no longer be repaired due to serious surface wear.
Excessive wear of the rollers not only reduces the forming rate of the pellet fuel and increases production costs, but also directly affects productivity. Therefore, how to effectively extend the service life of the pellet mill rollers is of great concern to the industry.
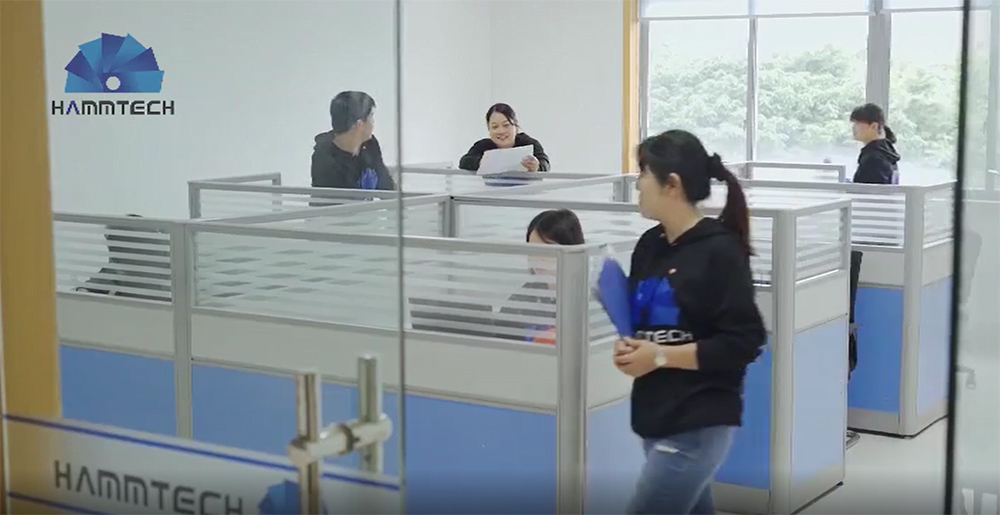
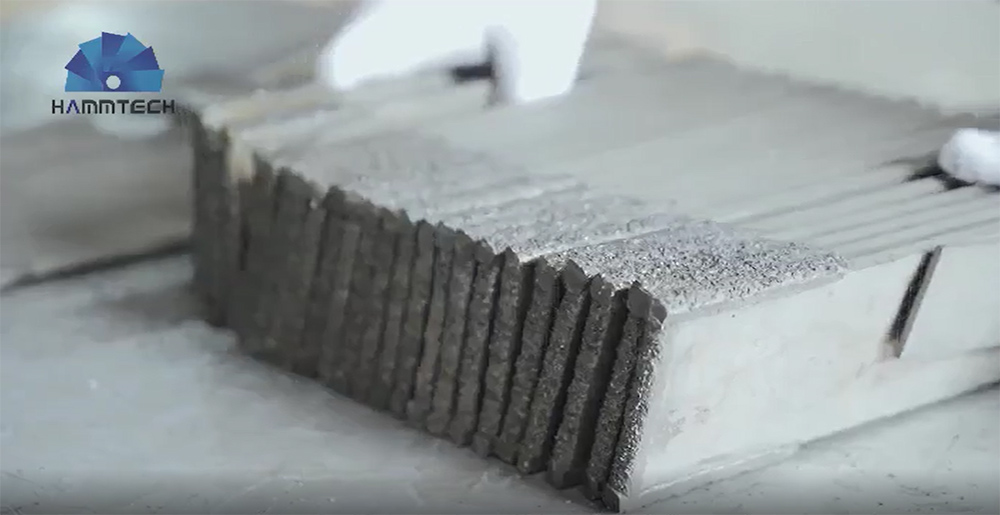

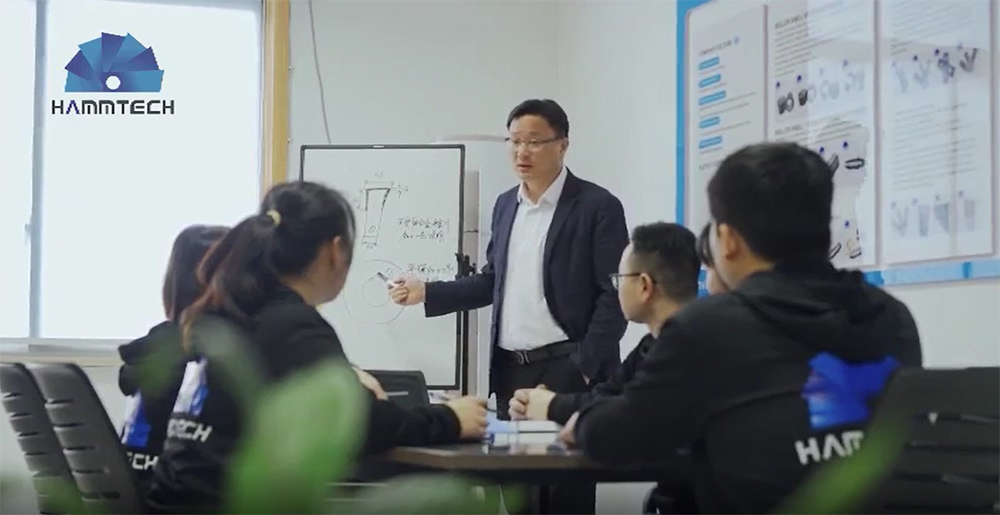
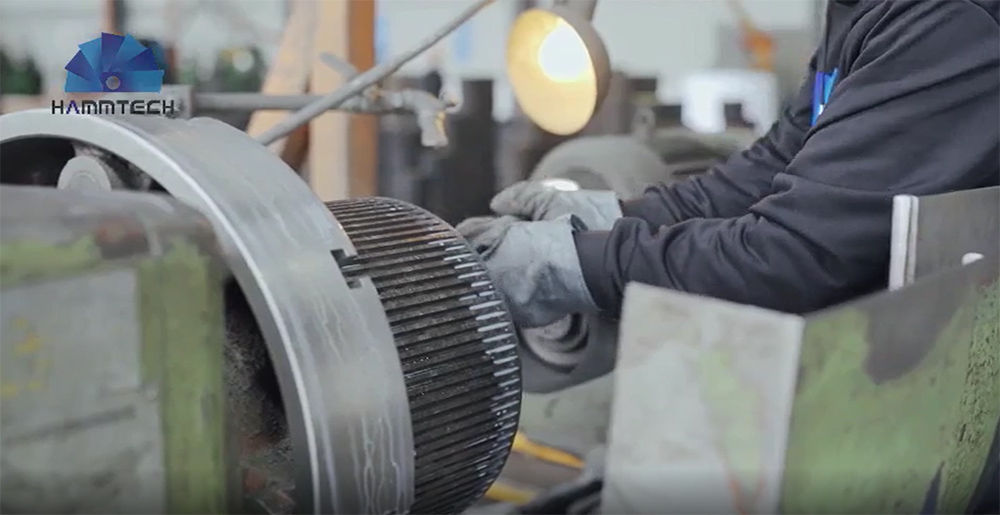
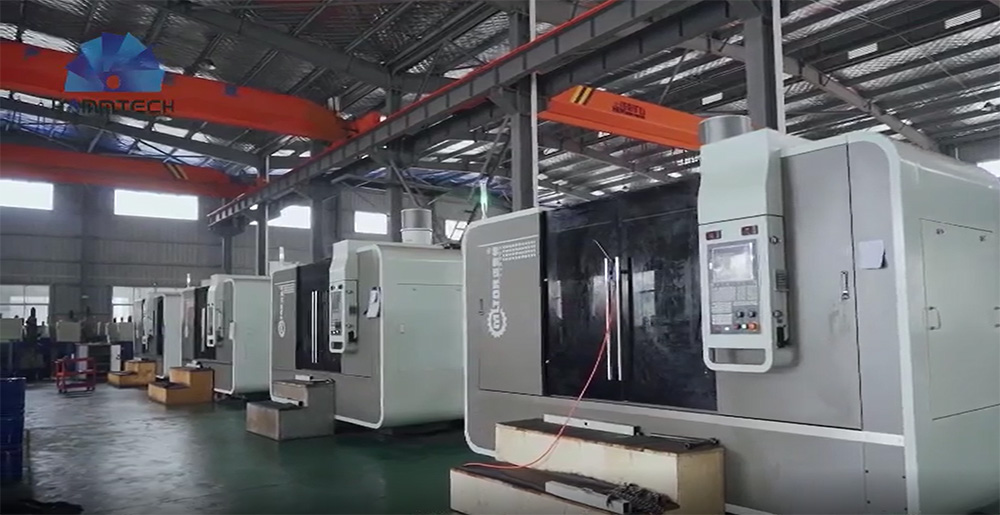